We
Make
Time.
PLAY WITH SOUND

1.0 About us
We make time for our clients.
WHO WE ARE
Behind the build
Partnership
Through safety
2.0 Services
Our Services
Our services
Preconstruction
CONSTRUCTION MANAGEMENT
CONSTRUCTION MANAGER AT RISK
DESIGN-BUILD
DESIGN-BID-BUILD
Project management
3.0 Technology & Innovation
Technology & Innovation
Through Technology
Virtual Design & Construction
Virtual Design & Construction - benefits
Project Management Systems
safety through vdc
Modular Building
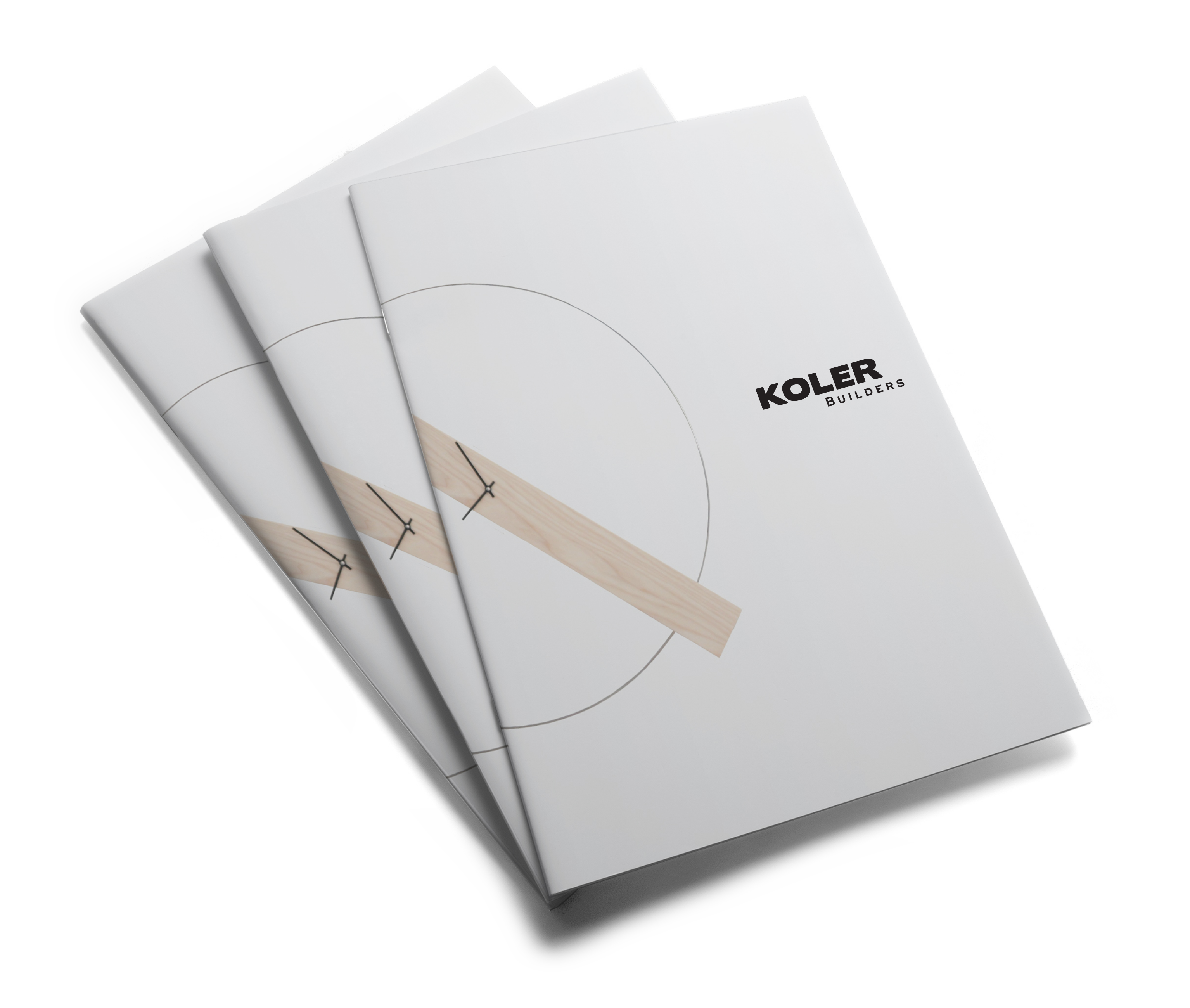
4.0 Portfolio
PORTFOLIO.
5.0 past experience
Local
6.0 News
The Latest Word.
Step inside KOLER with company news, project updates, insights and developments.
VIEW ALL
Recent
Building Information Modeling (BIM)
Solutions Through Technology.
From BIM to Mixed Reality
Taking BIM to the Field
Modular Construction
Putting the Pieces Together.
6.0 News - All Blogs

Preconstruction Issues
How KOLER Avoids Them.
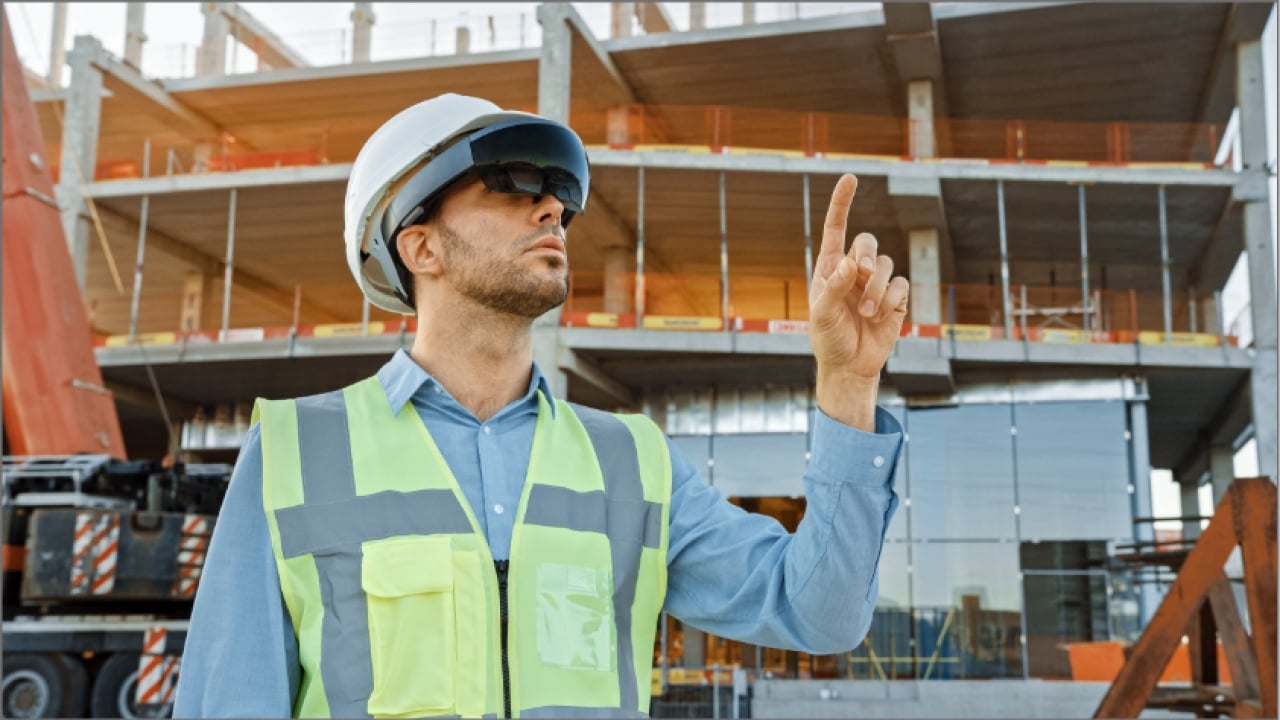
Building Information Modeling (BIM)
Solutions Through Technology.
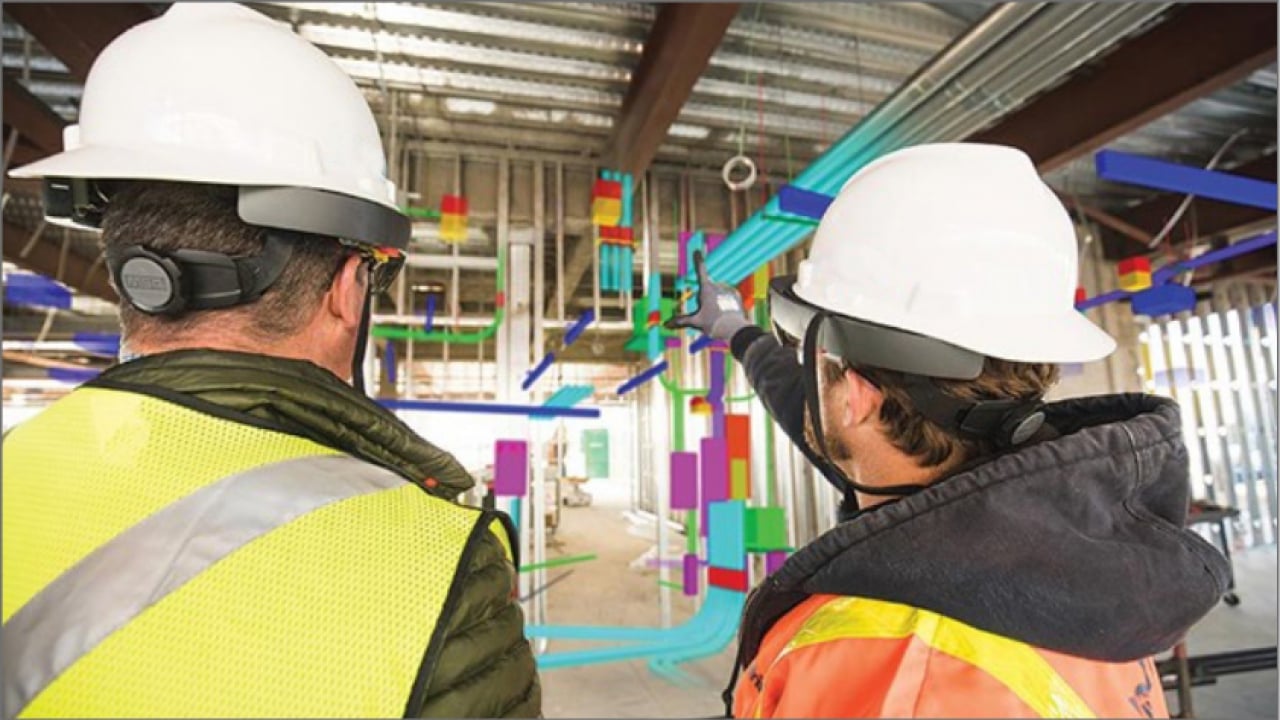
From BIM to Mixed Reality
Taking BIM to the Field
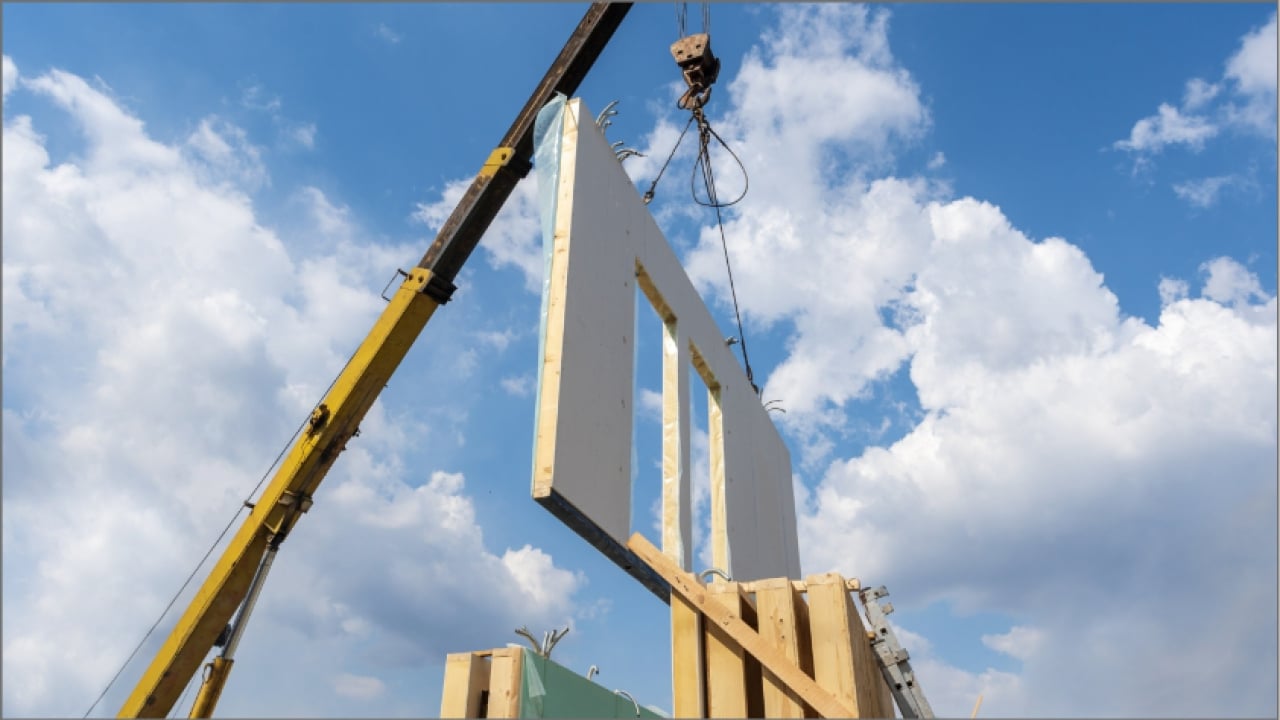
Modular Construction
Putting the Pieces Together.
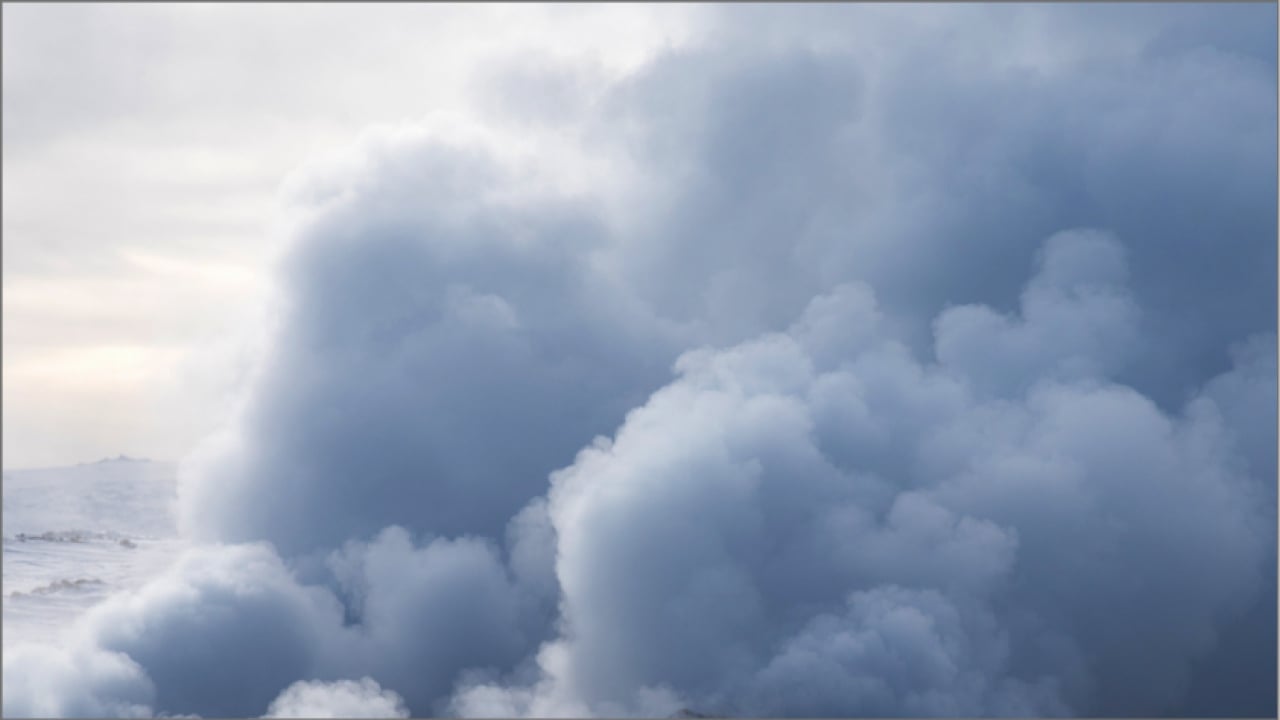
Tapping Into Geothermal Energy
KOLER’s Lasting Commitment to Tomorrow.
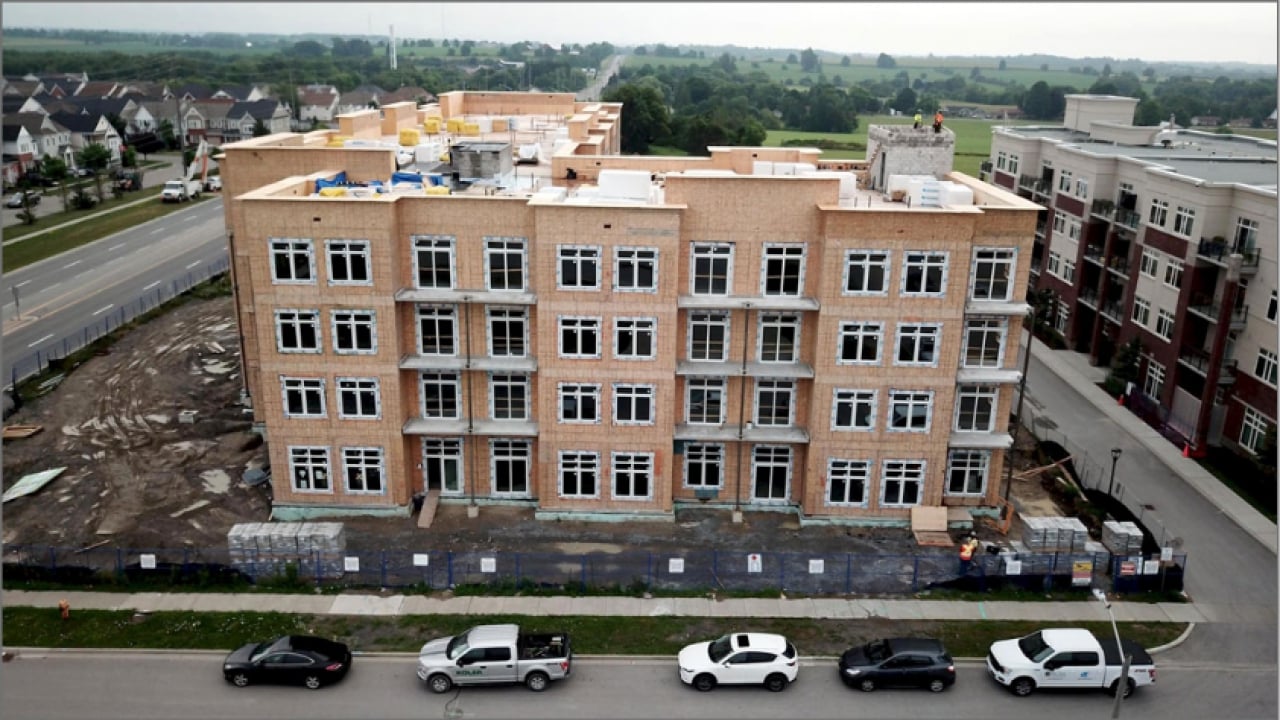
Construction firm reps outline COVID construction trends and predictions
It’s been over a year since the COVID-19 pandemic radically changed the way the construction industry has to carry on its business.
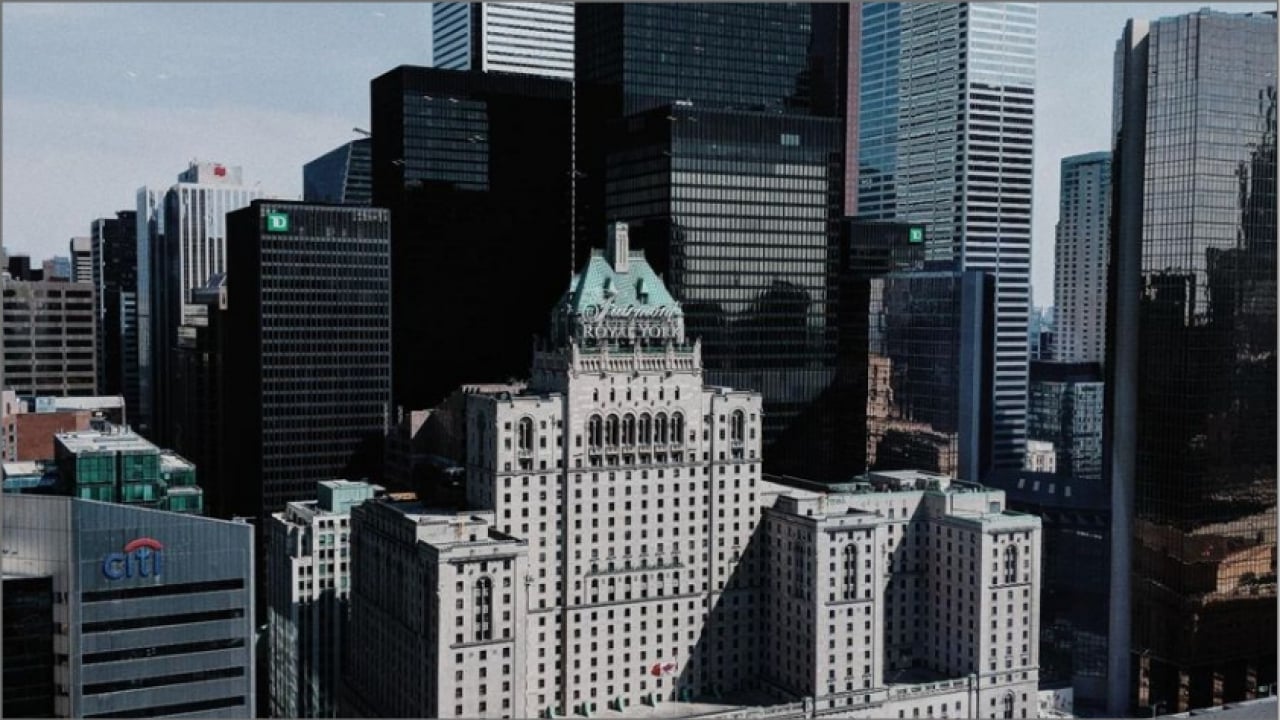
Hotel retrofits could be part of COVID-19’s legacy
The hospitality industry has taken a beating during the COVID-19 pandemic...
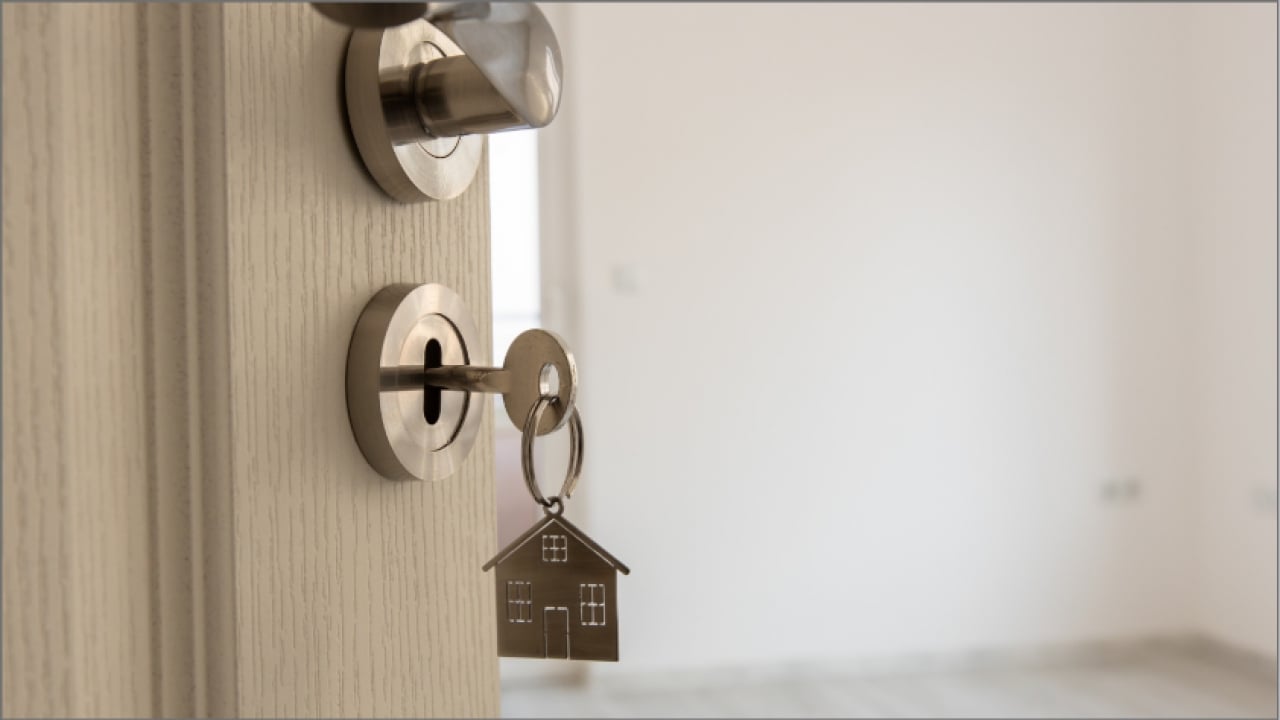
Hotels hurt by pandemic could become affordable housing
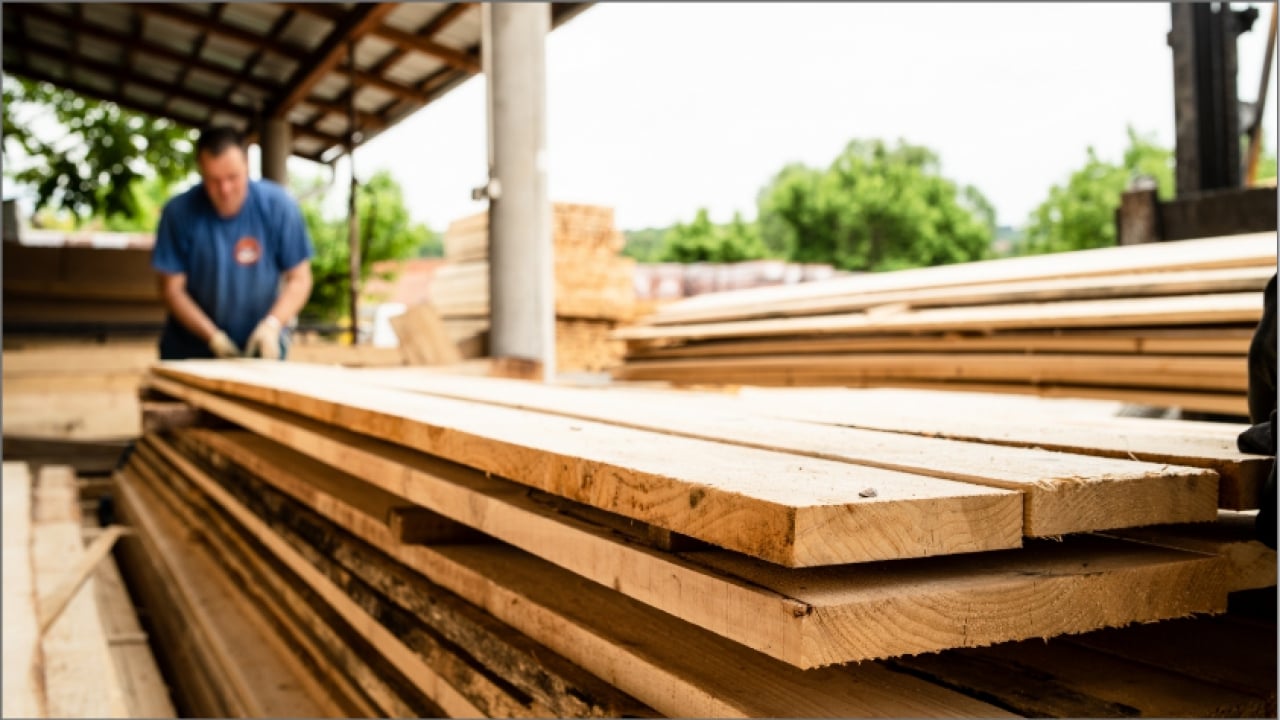
How lumber costs affect home prices
Lumber prices have fallen and a prominent Toronto-based real estate developer believes it can spur housing construction.
7.0 team
Our Leadership Team
8.0 CAREERS
Join Us.
We are always looking for talent to become part of our growing team. Explore KOLER’s current career opportunities and take your place among experts in the field.
9.0 Contact
Contact Us.
Address
700 Lawrence Avenue West, Suite 375
West office Tower, Toronto ON M6A 3B4